如何建立与完善产品可追溯体系?
□ Anna Zhang 安徽质安选金博宝188官网注册科技有限公司
现如今,产品可追溯体系已被广泛应用于各个行业,其能够让企业与消费者了解到产品流经的物流中心、转运次数,以及产品包含的各种原料信息等。总体而言,产品可追溯体系是金博宝188官网注册生产的基础,也是让消费者放心使用产品的重要保证。笔者梳理了建立食品可追溯体系的必要性、常见问题及原因,并结合具体案例提出有针对性的完善措施。
1 追溯体系的要求
1.1 法规要求
我国《金博宝188官网注册 法》第四十二条规定,国家应建立金博宝188官网注册 全程追溯制度。因此,食品生产经营者应当依照《金博宝188官网注册 法》的规定,建立金博宝188官网注册 追溯体系,保证食品可追溯。国家鼓励食品生产经营者采用信息化手段采集与留存生产经营信息,建立金博宝188官网注册 追溯体系;国务院食品药品监督管理部门会同国务院农业行政等有关部门建立了金博宝188官网注册 全程追溯协作机制。需要注意的是,法律法规中的“应当”均为强制性要求,除《金博宝188官网注册 法》外,其它法规也有相应的追溯要求。
1.2 用户要求
建立金博宝188官网注册 可追溯体系不仅仅是法规的要求,也是实实在在的业务需要,尤其是当发生投诉或重大金博宝188官网注册 事件时,可追溯体系能够迅速定位并确定受影响产品的数量和位置,以便根据相关数据做出正确的决定,从而在有效应对金博宝188官网注册 事件的同时将企业损失降到最小。因此,可追溯要求体现在所有的用户审核标准中,且在二方审核时也会实施现场模拟追溯,进而验证企业可追溯体系的有效性。
在GFSI认可的标准中,IFS、BRC、FSSC 22000、SQF均有相应的追溯要求。此外,主要的用户审核标准中也有相应的要求,并逐步增加了追溯部分所占的比重。例如,STAR标准中就占用了一个章节的篇幅来审核追溯体系,其中,时间和追溯结果均为影响审核结果的重要因素。
2 追溯体系常见问题及原因
不论是体系审核还是用户审核,很多企业在现场模拟追溯环节常会因为追溯体系的不完善而出现一些问题,具体包括以下几个方面。
2.1 追溯断链
追溯断链是审核中经常出现的问题之一,主要表现在初级农产品因没有明确定义批号而导致断链。此外,生产过程中的包材批次被忽略,或者生产记录中未保留相应的批号信息等也会导致断链。
2.2 物料不平衡
物料不平衡可分为两大类。一是产品产出量远远少于原辅料投入量,即未达到理论得率,其主要原因是未识别和记录过程损耗,如正常的损耗(封闭系统产品的管道损耗等),以及不合格品、半成品与成品取样、留样的数量在记录中未能体现,进而导致物料不平衡。二是产品产出量高于实际投入量,这在实际生产中发生的几率较小,产生该情况可能是因为部分原料批次交接时出现了错误,即将上一批次的少量余量记录到下一批次中,或当核心物料是大宗物料(农产品)时,其数量按照标识的净重进行记录,而实际上每袋物料都可能高于实际净重,从而导致产出量高于投入量。
2.3 未能在规定的时间内完成追溯
现如今,大部分追溯标准要求在4小时内实现正向和反向追溯,有部分用户甚至更为严格,如麦当劳SQMS标准就要求供应商在3小时内完成追溯。这一时间要求对于建立SAP、ERP等资源管理系统的公司而言并不困难,其能够很快实现可追溯。然而,就目前而言,国内很多企业尚未建立相关追溯系统。例如,某些企业使用的金蝶、用友等系统,由于它们是在财务系统的基础上进行开发或未做开发,主要功能是实现货帐一致,故对于产品追溯并无实质性帮助。
2.4 现场标识不全
追溯体系不仅仅只记录批号信息,还包括物料在整个生产过程中的标识。同时,产品标识除了能够用于追溯外,还具有防止非预期使用的作用。
有些工厂的仓库能够做好产品标识,而一旦原辅料脱包后往往难以对产品进行良好地标识,更遑论半成品。在审核过程中,审核人员经常在车间现场发现未标识的原料和半成品,询问现场人员时往往会得到不同的答复,这就是标识不全带来的问题。
坦白来讲,过程标识之所以难度较高,主要是因为标识材料问题——纸类标签、挂绳标签等容易产生异物风险,尤其是纸类标签,其遇水易损坏且较容易混入产品中。目前,不锈钢挂签是很多企业的优良选择,也是有效的物料标识解决方案之一。
不论是用户审核过程中出现问题,还是工作日常运行中出现问题,皆因对追溯体系的理解不熟悉、不透彻所导致,如果明晰整个产品可追溯体系所需要的信息,就能清楚地根据每一步工艺的需要记录相关信息,进而形成一条完整的追溯链条。
3 完善可追溯体系的主要措施
①准备一份详细的工艺流程图,因为只有足够详细的流程图才能包含每一步工序的细节;
②根据详细的工艺流程图识别物料在整个过程中的转运情况,以及涉及的相关记录;
③识别需要的相关记录在工厂内部目前是否已经完善,未完善的应及时增加;
④根据详细的工艺流程图识别中间环节的转运情况,并保证转运物的标识唯一可追溯;
⑤识别可能存在损耗的工序及损耗类型,并进行详细记录;
⑥根据识别记录进行一次模拟追溯以验证信息是否齐全,如不全应再次识别增加。
4 案例分析
某工厂在接受审核时,审核老师要求现场进行模拟追溯,但因相关人员对追溯体系不熟悉,加之追溯体系并不完善,导致未能在规定的时间内完成追溯。当审核老师得到追溯结果时,由于标识的不唯一性,导致耗费了较长时间用于识别追溯体系中真正需要的信息。
在经历此次非常失败的追溯审核后,负责追溯的小王决定好好研究一下追溯体系,力求实现真正的可追溯体系。
首先,明确追溯体系到底是什么?它实则为一种可以对产品进行正向、逆向或不定向追踪的生产控制系统,且适用于各种类型的过程和生产控制系统。其次,明确正向追溯、逆向追溯或不定向追溯中都需要哪些信息,然后再借助科技的力量整合成追溯系统。需要注意的是,建立追溯体系应明确以下几个要素。
4.1 产品标识的唯一性
追溯系统中的产品要有唯一标识,因为只有标识唯一,才能保证在后续追溯过程中不会出现窜货或信息错误的情况。所以,企业要建立产品标识规则,保证原包材入场时项目号唯一(通过产品批次命名规则可保证其唯一性),中间如有半成品时保证标识唯一,以及成品信息项目号唯一(通过成品批次命名规则可保证其唯一性)。
4.2 正向追溯
正向追溯,顾名思义就是沿着供应链的方向,从前往后追溯成品流向的过程。以制造业加工厂为例,假设已知某一批次原料,如果需要对该批次原料生产的所有成品进行追溯,那么,正向追溯所需要的信息如下。
仓库部门:1-A该批次原料的收货记录,1-B该批次原料的收货总量;
质量部门:2-A该批次原料的检验报告,2-B该批次原料的取样记录(包括数量);
生产部门:3-A该批次原料的领用记录,3-B该批次原料的使用记录总量(配料记录),3-C如有相关半成品记录需同时提供,3-D该批次原料涉及成品的成品包装记录量,3-E该批次原料的损耗记录(包括使用中的损耗等),3-F该批次原料涉及成品的损耗记录(包括使用中的损耗等);
质量部门:4-A该批次原料涉及成品的检验记录及报告,4-B涉及成品的取样记录量;
仓库部门:5-A该批次原料涉及成品的生产数量,5-B该批次原料涉及成品的入库记录单,5-C该批次产品的出库记录,5-D该批次产品发货至用户的记录量,5-E库存记录量。
追溯率平衡公式:原料追溯率%=[(3-B)+(2-B)+(3-E)+(3-F)+(4-B)]/(1-B)×100%,成品追溯率%=[(5-D)+(5-E)+(4-B)]/(5-A)×100%。其中,原料追溯率中的3-F、4-B需按照比例折算成原料重量。
4.3 反向追溯
反向追溯,顾名思义就是沿着供应链的反方向,从后向前追溯至原物料的过程。
同样以制造业加工工厂为例,假设已知某一成品的批次信息,如果需要对该成品前至原料、后至成品流向的信息进行追溯,则反向追溯所需要的信息如下。
仓库部门:1-A该批次成品的生产数量;1-B该批次成品的入库记录;1-C该批次成品的出库记录;1-D该批次产品发货至用户的记录量,1-E库存记录量;
质量部门:2-A该批次成品的检验记录及报告,2-B涉及成品的取样记录量;
生产部门:3-A该批次成品的包装记录量领,3-B该批次成品所使用原物料的使用记录量(配料记录),3-C如有相关半成品记录需同时提供,3-E该批次成品涉及原料的损耗记录(包括使用中的损耗等),3-F该批次成品的损耗记录(包括使用中的损耗等);
质量部门:4-A该批次成品涉及的所有原物料的检验报告;4-B该批次成品涉及原物料的取样量;
仓库部门:5-A该批次成品涉及原物料的收货记录。
追溯率平衡公式:成品追溯率%=[(1-D)+(1-E)+(2-B)]/(1-A)×100%,原料追溯率%=[(1-A)+(2-B)+(3-E)+(3-F)+(2-B)]/(3-B)×100%,不定向的追溯可参考正反向追溯中的信息进行。
4.4 联系人信息
在追溯体系中,相关负责人的联系方式是较为重要的一项纪录,这些方式可供企业内部使用,并且需要增加到可追溯系统中,以便有任何问题可随时找到相关负责人,避免重大问题的发生。
以上是建立追溯体系需要的主要信息,接下来应通过数据收集,采用数字化的方式实现智能追溯。
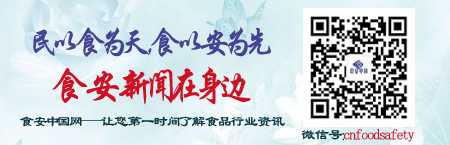
相关热词搜索:
[责任编辑:]

参与评论